Results for Pulp Machines
Over the years we have learned the following important points about steam application to Pulp machines:
Research has shown that there is a 1% increase in web dryness for every 18 F increase in sheet temperature.
Research has also shown that a production increase up to 4% theoretically results from a 1% increase in web dryness to the dryer. This means there is much impetus to heat the web early in the paper making process.
There are various ways to heat the sheet, but one of the most efficient is with steam.
The best steam shower locations for any Pulp Machine are the Fourdrinier flat boxes, followed by suction press nips.
Any profiler should be used to improve moisture uniformity, especially important for Fluff Pulp. To increase dryer-limited production or reduce dryer steam demand, a Lazy Steam Injector should be used in suction press nips to uniformly heat the sheet and enhance water removal.
Generally, uniform steam application at the press is more efficient than using the same steam on the Fourdrinier. It is possible that proper use of a Fourdrinier steam shower will remove as much steam from the dryer as the steam shower is supplied with.
By contrast, a Lazy Steam Injector in the press section will typically reduce the dryer steam demand by at least 50% as much steam as the injector is supplied. For instance on a machine making 50 tph supplying a well operated Lazy Steam Injector with 7,500 lbs/hr will remove at least 3,750 lbs/hr from the dryer.
Most mills, however, with dryer-limited machines, would much rather increase the production rate than save a modest amount of steam. In these cases steam application can improve the production rate significantly.
Heating just the press felt (and not the sheet) can increase production by up to 2% by allowing a press load increase without crushing, thus increasing the web dryness and reducing the dryer load.
Downstream of a profiler, sheet surface temperatures as high as 180 to 190 F should be expected when applying the full amount of steam recommended.
On machines like Fluff Pulp that cannot tolerate the bulk reduction caused by directly heating the web it helps to heat the press fabrics just enough to offset the web temperature loss into the dryer that would otherwise occur. It should be noted that a hot sheet compresses easier than cool sheet so if pressed some compaction will occur.
Steam application is especially helpful on "cold" machines where the decrease in water viscosity is so much greater than at the high end of the temperature spectrum.
Results vary by machine, but, in one Pulp machine, 1000 lbs/hr steam increase to the 1st Press Lazy Steam Injector reduced the Flakt Dryer steam demand by 6000 lbs/hr.
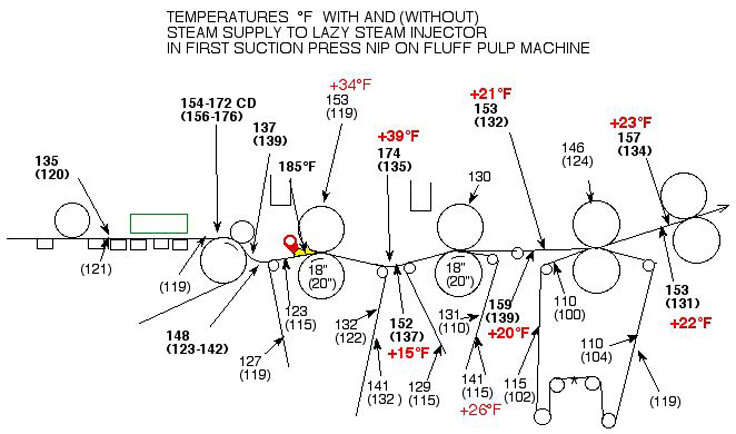
Typical temperatures on a Fluff Pulp machine with Lazy Steam Injector into 1st Suction Press nip (red denotes temperature increase "with" steam injection). The temperature at the Smoothing Press increased more than 20 F, giving a production increase of more than 3%. A second injector at the 2nd Press yielded an additional 2% production increase, all for a minimal investment. The payback period for this project was less than 8 weeks.
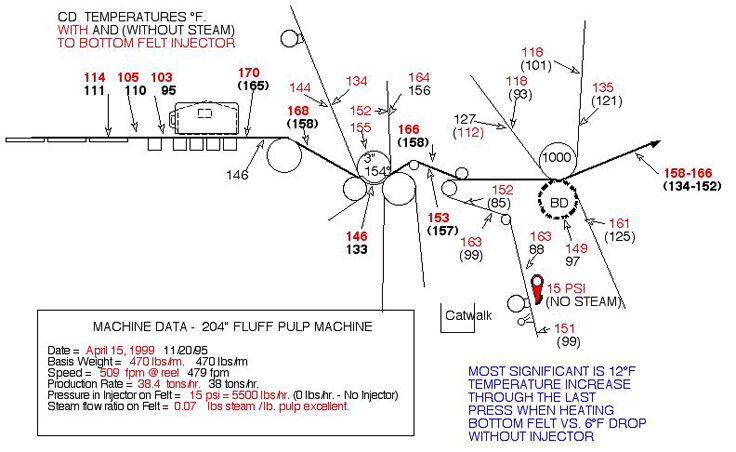
On this bulk-sensitive Fluff Pulp machine the last press bottom felt was heated. Instead of the sheet losing temperature through the last press, the temperature actually increased. This installation was reportedly worth 1.5 tons/hour production rate. Mill personnel did not observe any bulk reduction problems. Red denotes temperatures "with" steam injection.
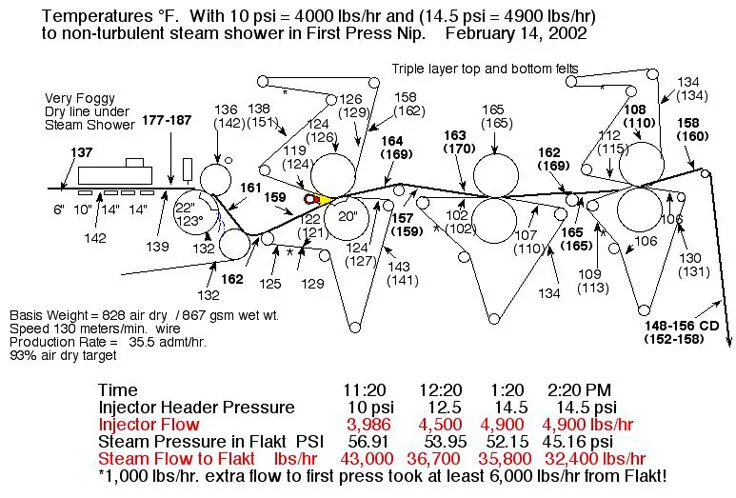
A Market Pulp machine with a Lazy Steam Injector in the Double-Felted Suction 1st Press nip. Optimizing low pressure steam flow to the injector gave dramatic steam savings in the Flakt dryer, removing at least 6000 lbs/hr high pressure steam load.